Quality Control
At PKCELL, every battery undergoes rigorous testing at each stage of production, ensuring superior performance and safety.
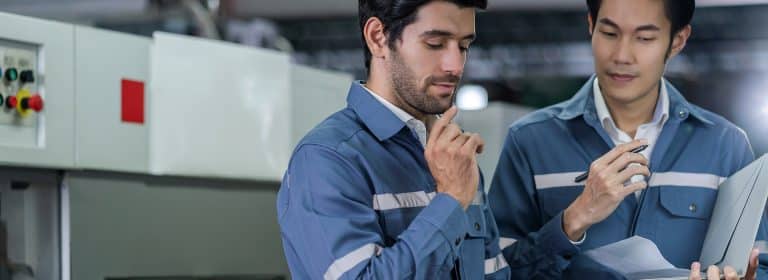
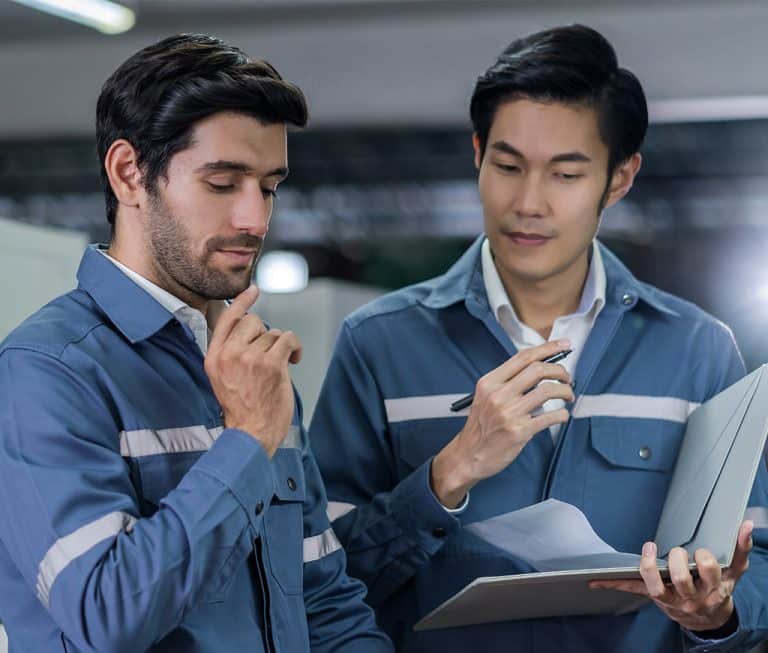
In the field of battery manufacturing, quality control is a key link in ensuring product safety and performance. PKCELL adopt a series of meticulous inspection processes, from raw material warehousing to finished product shipment, and every step is strictly monitored. Through advanced production technology and automation equipment, combined with a comprehensive traceability system, we can quickly locate and solve any quality problems. We are committed to meeting the high standard needs of global customers and providing safe and reliable battery products through continuous quality management and innovation.
Battery Quality Control Process
We are committed to continuously optimizing product performance and safety standards through precise quality control processes to meet the high standards of global customers.
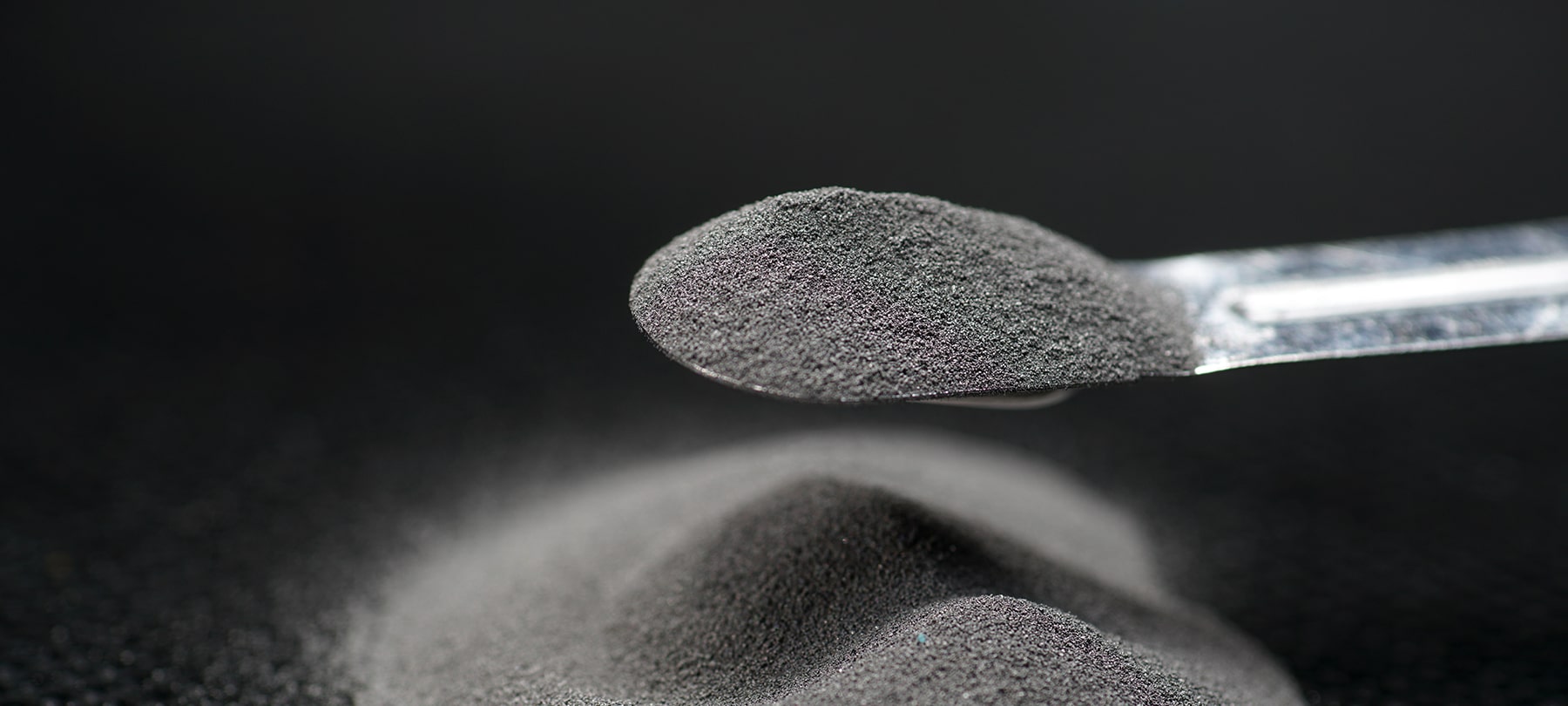
Raw material
inspection

-
PurposeTo ensure all raw materials meet required specifications before entering the production process.
-
Step1.Conduct sampling testing on battery positive and negative
electrode materials, separators, electrolytes and other raw materials.
2.Check physical and chemical properties, including purity and stability.
3.Nonconforming materials must be returned to the supplier.
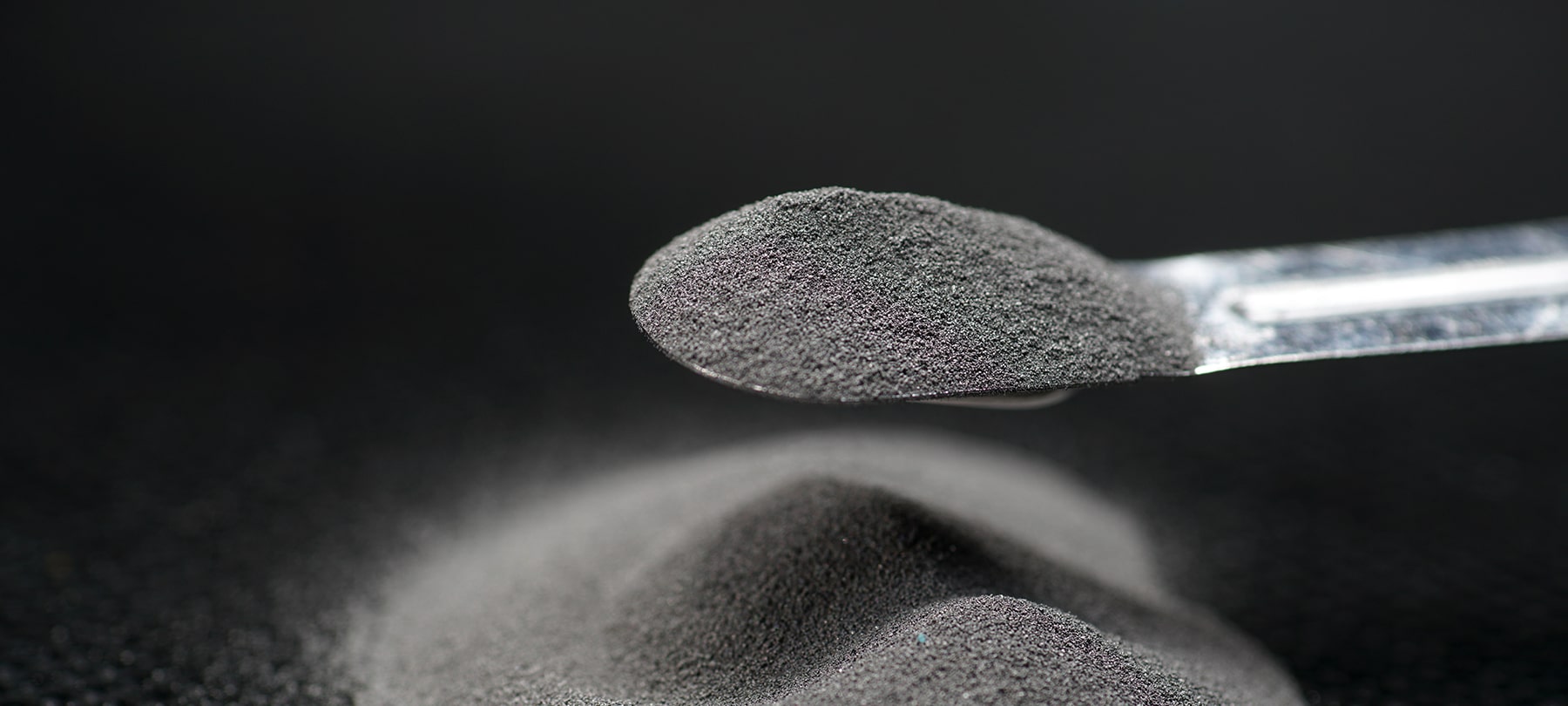
In-Process Quality Control

-
PurposeTo monitor and control the production process to prevent defects and ensure product consistency.
-
Step1. Implement real-time monitoring and quality checks at each production stage (mixing, coating, winding, assembly, etc.).
2. Control process parameters, equipment conditions, and the performance and appearance of semi-finished products.
3. Identify and correct any deviations from the standards promptly.
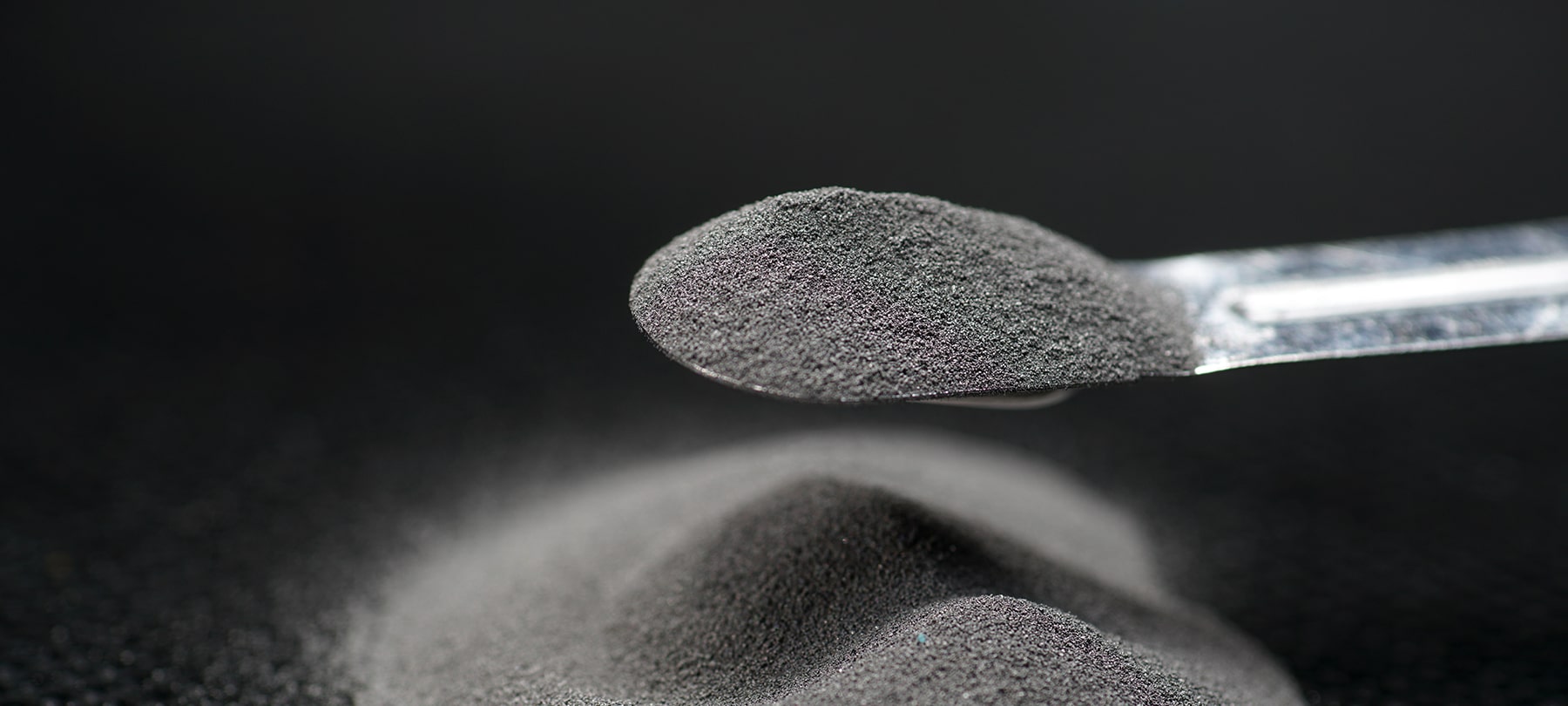
Finished Battery Testing

-
PurposeTo verify that finished batteries meet design requirements and safety standards.
-
StepConduct comprehensive performance tests on finished batteries, including capacity, voltage, internal resistance, self-discharge rate, cycle life, overcharge/over-discharge protection, short circuit protection, high and low-temperature performance, vibration, shock, and drop tests.
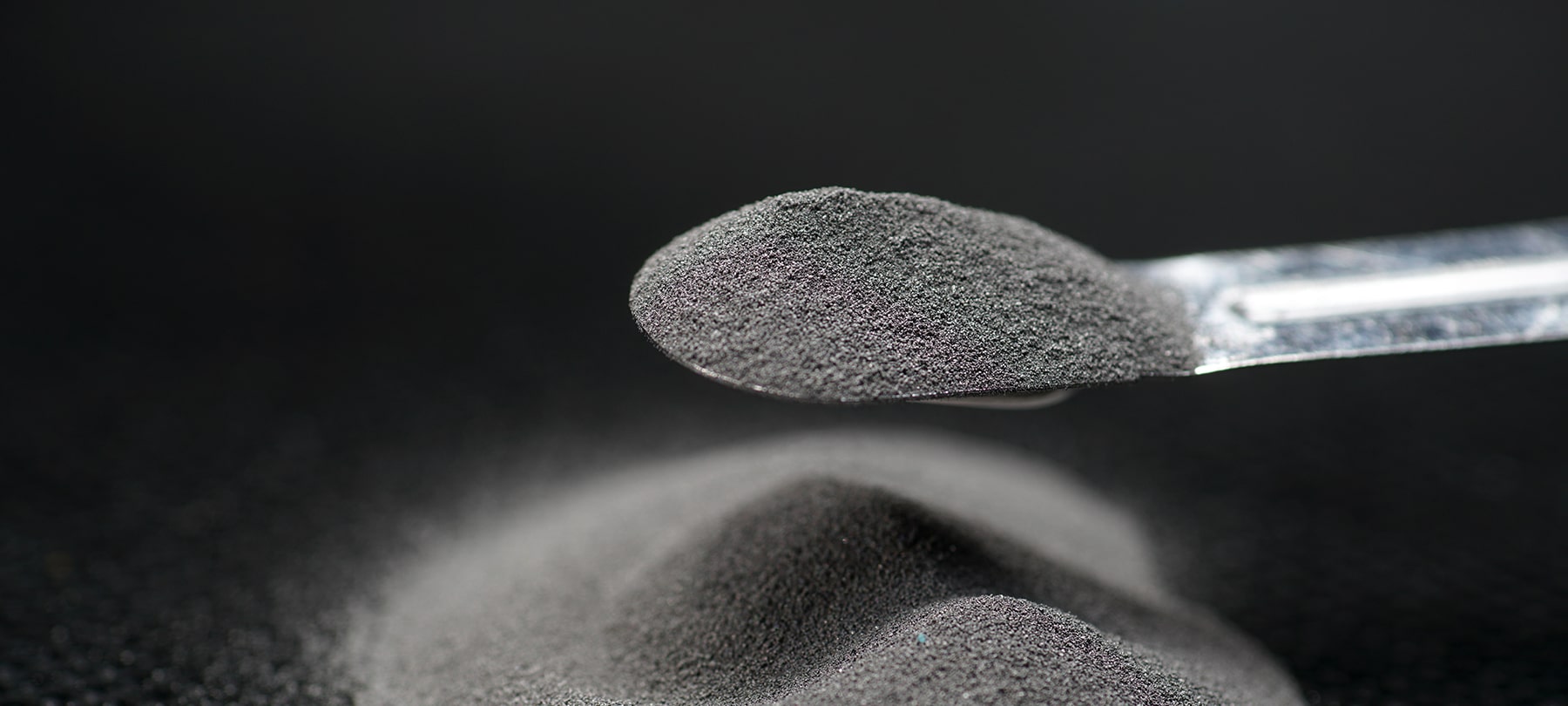
Aging Testing

-
PurposeTo evaluate long-term stability and reliability by simulating real-world aging conditions.
-
Step1. Subject a sample of finished batteries to prolonged aging tests under accelerated conditions (high temperature, high humidity, etc.).
2. Assess battery performance and degradation over time.
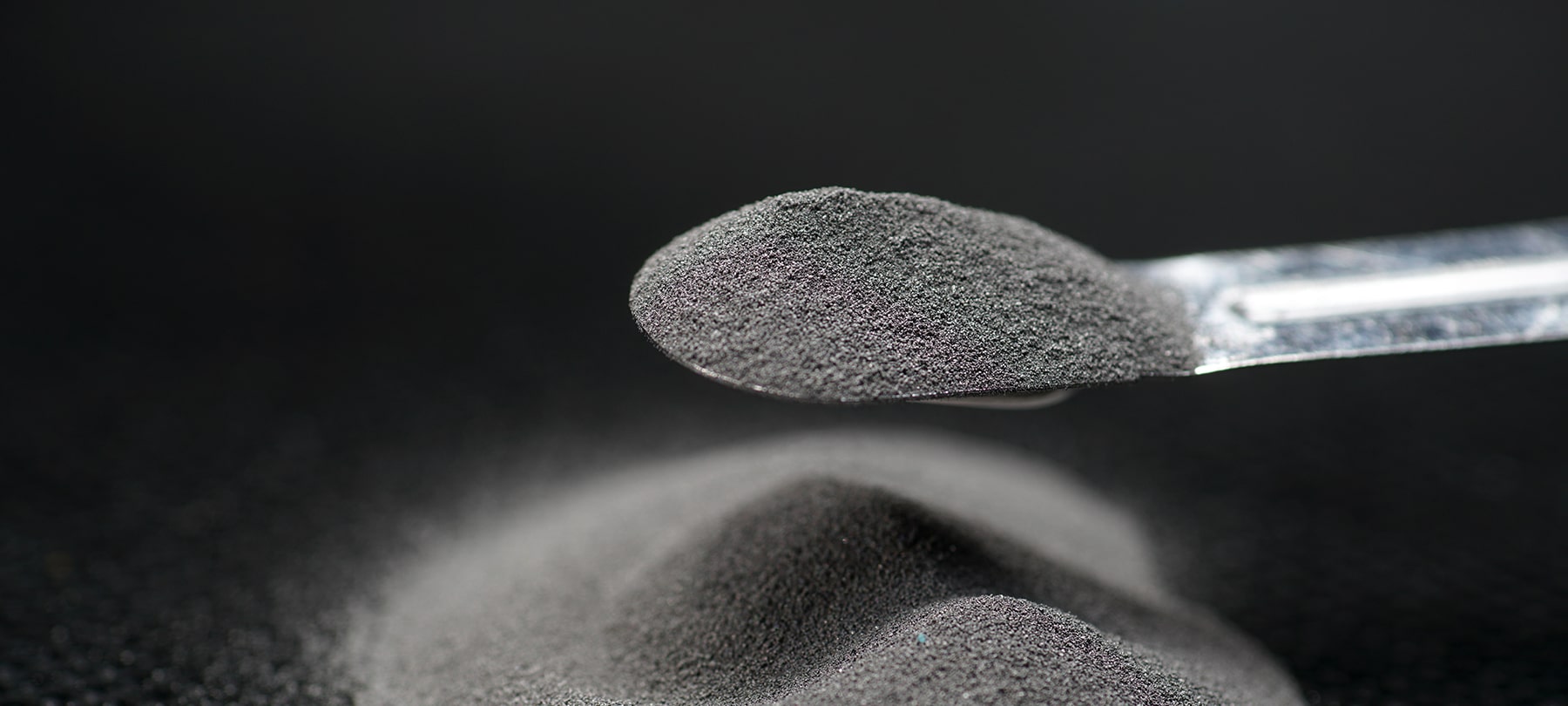
Final inspection
and shipment

-
PurposeTo ensure that only products meeting all quality and safety standards are shipped to customers, and that they are packaged and shipped correctly to prevent damage during transit.
-
Step1. Conduct a final visual inspection of the finished battery packs to check for any cosmetic defects or damage.
2. Perform random sampling and conduct functional tests to verify performance and safety compliance.
3. Compare product specifications against quality standards and customer requirements.
4. Reject any battery packs that fail to meet the criteria.


Raw material inspection


Production process imonitoring


Finished Battery Testing


Aging Testing


Final inspection and shipment
Get in Touch
You can reach us by phone, email, or by filling out the contact form below. We aim to respond to all inquiries within 24 hours.
-
Phone+86 13925223326
-
E-mail
-
Company address9th Floor , Block B, Hongrongyuan North Station Center, No. 328, Mintang Road, Longhua District, Shenzhen,China,518110